|
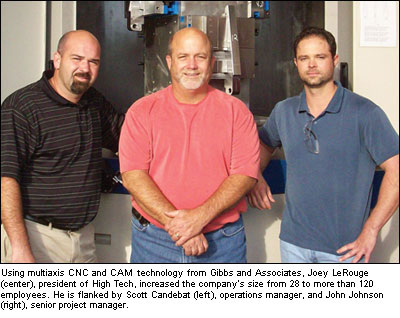
Joey LeRouge has followed a familiar path in starting his own company, graduating from his own garage to a fully equipped 9200 ft2 (855-m2) manufacturing facility located in Broussard, LA.
While employed at a well-head company, LeRouge started High Tech Components in 1987, distributing highpressure gate valve parts to oil drillers. He relied on local machine shops to supply the manufacturing. As his business grew, however, suppliers were unable to keep up, so he bought a manual lathe and started making parts himself. The business continued to grow in a new facility, but cycles in the oil industry made business growth unpredictable. To flatten the ride, LeRouge turned his distributorship into a job shop.
By late 2001, High Tech had several manual machines, three CNC machines, and 20 employees in its facility, where it faced new challenges related to programming. The CNCs had to be programmed manually, making complex parts cumbersome to program. In addition, the chief programmer planned on leaving.
For the shop's next phase of growth, LeRouge focused on NC programming. Because his shop was far from industrial centers where assistance might readily be available, he looked for CAM software and chose GibbsCAM's Basic Milling from Gibbs and Associates (Moorpark, CA) for its ease of use and popularity locally in the Lafayette parish.
A key hire in early 2002 was made when John Johnson, a recent mechanical engineering graduate, joined the company. Johnson was trained in shop operations, including NC programming, which would become one of his main responsibilities. Because the CNCs had conversational controls, the CAM system was mostly left unused until two years later when the shop purchased a CNC mill with a nonconversational Fanuc control, which presented its own kind of challenge.
"That's when the software came in handy," says Johnson. "I had already taught myself to do basic milling with GibbsCAM, so we got that mill up and running fast, without having to learn that control, and we started to rely on the software for 2.5-axis milling."
Things changed again three years ago, when a prospective customer approached High Tech Components with a more complex part, a universal casing elevator slip, asking for a low price. Seeing the prospect as an opportunity for much greater business, LeRouge took the risk and accepted the challenge.
The universal casing slip is so called because it is used in various applications within the casing elevator, an assembly used by drill rigs for lifting, lowering, and applying torque to pipe. The elevator is a family-of-parts assembly that High Tech produces for various oil drilling customers. Its main component is a round bowl, with a large outer diameter and tapered internal diameter. A dozen parts fit within and around the tapered ID, with outer radii perfectly matching the ID's taper.
Slips are inserted within the bowl, together with dies, which have an extruded-dovetail shape on one side, and grooved teeth on a radius to fit specific pipe diameters on the other. When these internal parts are hydraulically lifted or lowered, they open or close onto the pipe, releasing or gripping it. Different configurations perform specialized functions, some to lift and lower pipe, others to tighten and loosen connections, while others do both.
"With my limited experience, the part did not seem like something we could make easily," admits Johnson. "We tried six or seven different ways to make it, using fixtures, conventional methods, and custom tooling, exhausting every option."
High Tech had not moved beyond the 2.5-axis Basic Milling GibbsCAM software, so the part's radiused cut on a taper required custom tooling. However, none of the setups were sufficiently rigid because the parts were supported with dovetails. "It was a complete nightmare," Johnson says. "After all that trouble, we purchased the GibbsCAM SolidSurfacer and Advanced Mill modules, which gave us many more options for tackling that part."
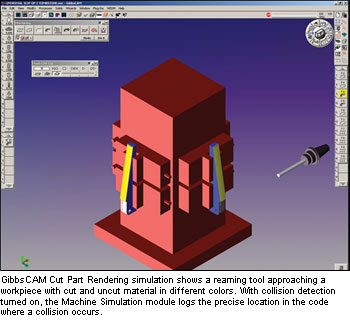
They had tried making the part with 2.5 axis, in four operations. Advanced Mill and SolidSurfacer allowed using a fixture on a vertical mill, and doing it in four-axis and two operations, but this lacked rigidity, so they returned to 2.5 axis with a different setup.
By then, High Tech had received a big blanket order from the customer. For efficiency, a setup was developed to allow loading raw stock and finishing the part with four operations in a single cycle on one machine. "The new software modules easily facilitated the various approaches," says Johnson.
With the earlier process of multiple setups, High Tech would run hundreds of parts through the first operation, then set up to run the second, and on through the fourth. At month's end, they would have an inventory of unfinished parts, but without completed parts, there would be no payment. The newer, single-cycle process enabled making a finished part with each cycle, which provided payment for all production work at month's end, leaving no inventory of unfinished parts. "It wasn't the most productive way of making large quantities, but we were paid monthly," Johnson says. "and we did that for a long time."
Then orders for similar parts of different sizes were received, and High Tech used the same setup and programming methods, with all the flexibility that the software provided. They didn't see those parts again until a year ago, by which time they had purchased four-axis horizontal mills, which provided opportunities for increased efficiency.
Advanced Mill and SolidSurfacer software made programming and indexing in four axes efficient and helped reduce cycle times. Furthermore, the software's solid modeler enabled Johnson to model the exact stock and tooling to be used, so he could verify toolpaths and check for uncut material, gouging, interference, and collisions.
With four-axis machining, four slips at a time are run, one on each side of a tombstone. The irregular stock has five plasma-cut sides at different angles. By accurately modeling stock in GibbsCAM, and dynamically rendering the toolpath with the software's Cut Part Rendering, he ensured proper machining and saved a lot of time in program prove-out.
"The software provides many ways to set up for toolpath rendering and collision detection," Johnson explains. "The rendering records exactly where a collision occurs, so you can fix the problem without stepping through the entire program. It's especially useful for long programs with many tools and operations. I use Cut Part Rendering for everything, and I won't put a program on the machine without it."
Johnson says there are multiple features of the software that have made efficiency easier to achieve, not just for the universal slip, but for many other parts High Tech has made since first taking a risk to gain a large customer. "When we had the final 2.5-axis method running well, we finished six parts a day. With the horizontal mill, we get 20 or more."
Frank's International has become the shop's largest client among many, which include Halliburton, Wood Group Pressure Control, Weatherford International, and Pathfinder Energy Services, all oil drillers. According to LeRouge, the shop is now the most diverse in machining capability in the region, perhaps in the whole state. He has invested in training his people in management and operations, and High Tech will soon become the only Louisiana shop with an apprenticeship program.
Operating in three adjacent buildings, High Tech has grown from 28 employees to over 120 in three years, and from 6 to 21 CNC machines, including several four-axis mills, a five-axis Okuma, and a nine-axis Daewoo MX2500 ST multitasking center with two live-tooling turrets and two spindles. All machines are driven by five seats of GibbsCAM on a network. The company employs ten NC programmers of various levels of expertise. Johnson says that over 99% of all these resources serve oil drilling companies.
Within months, High Tech will be taking delivery of three new vertical lathes, in part to accommodate a customer that wants parts with an 80" (2-m) diam. To house the additional equipment and facilitate growth, the shop is adding 30,000 ft2 (2787 m2) with the construction of another building.
LeRouge attributes a good part of success to technology. "It has been challenging keeping up with technology," he says, "but Gibbs and Associates has been a great partner and an alliance that works very well. They provide a common interface for every machine we choose, and allow adding the modules we need as we continue to grow. While John has become a first class, top-notch programmer, I know the value of GibbsCAM. It helps us expand and stay ahead of everybody else."
Reprinted from Manufacturing Engineering. February 2009 Vol. 142 No. 2 |
|